The Plan-Do-Check-Act (PDCA) Cycle is another way of looking at problems and determining appropriate solutions. The PDCA Cycle is often called the Deming Cycle because it is about continuous process improvement.
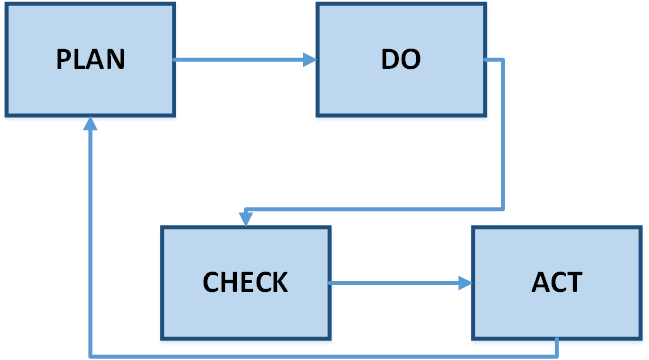
Exhibit: PDCA Cycle
Here is what happens in each phase:
Plan: In this phase, the team identifies a business problem and agrees on the problem. The team then analyzes the business problem to determine the root cause of that problem. Cause and effect diagrams might be used in this phase. The process associated with the problem area is mapped out to look for gaps.
Do: In this phase, the team generates a number of potential solutions to the problem. The solutions are narrowed down to a few, and then evaluated further to select the best solution to the problem. This solution is then pilot tested to ensure it solves the problem.
Check: In this phase, the pilot test of the solution is evaluated to see if it worked. Adjustments are made as needed to ensure a better solution. If necessary, another pilot test is conducted (especially if significant adjustments have been made.)
Act: In this phase, the solution is implemented more widely and processes are updated along with any documentation.
And here is where the PDCA Cycle is a bit different. In a culture of continuous improvement, the team goes back and looks for other potential area of improvement, again following the PDCA Cycle (as shown in the exhibit above.)